How to Move Production from China to India: A Complete Guide for 2025
Global businesses have increasingly reconsidered their reliance on China as the world's primary manufacturing hub. One prominent shift in recent years has been the move from China to India. India is not just an alternative but as a strategic production base that offers long-term advantages in cost, scale, and stability. This guide walks you through the key considerations, steps, and strategies for successfully relocating production from China to India.
Why Consider Moving from China to India?
Before diving into the logistics, it's important to understand the strategic motivations behind this shift:
- Cost Efficiency: India offers lower labor and operational costs compared to China's increasingly expensive industrial zones.
- Geopolitical Stability: Ongoing trade tensions between China and the West have encouraged companies to seek politically neutral environments like India.
- Government Incentives: The Indian government has launched schemes such as “Make in India” and the Production-Linked Incentive (PLI) program to attract foreign manufacturers.
- Growing Infrastructure: India is rapidly improving its industrial parks, ports, and logistics corridors to better support global manufacturing.
- English Proficiency: Widespread use of English in business and legal environments eases communication and reduces translation errors.
Key Considerations Before the Move
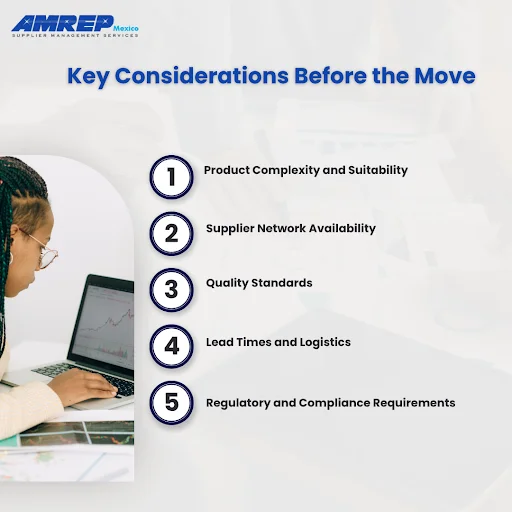
Relocating your supply chain is not just about changing geography. It requires deep planning and analysis:
1. Product Complexity and Suitability
Not all products are ideal for manufacturing in India. Complex electronics or items requiring a highly specialized supply chain may still face challenges. Start with feasibility studies and pilot runs for less complex products.
2. Supplier Network Availability
India’s supplier ecosystem is growing but may not be as mature as China's. You’ll need to map your current bill of materials and identify equivalent or better local suppliers for key components.
3. Quality Standards
Indian manufacturers can meet international standards, but consistent quality assurance processes must be built into supplier agreements. Include clear quality control plans, inspections, and certification requirements.
4. Lead Times and Logistics
India’s logistics network is improving, but you should factor in transportation times, customs procedures, and port infrastructure when recalculating your supply chain model.
5. Regulatory and Compliance Requirements
Understand India's tax laws, import-export regulations, labor laws, and environmental policies. Consider partnering with a local compliance expert or agency.
Steps to Successfully Relocate Production
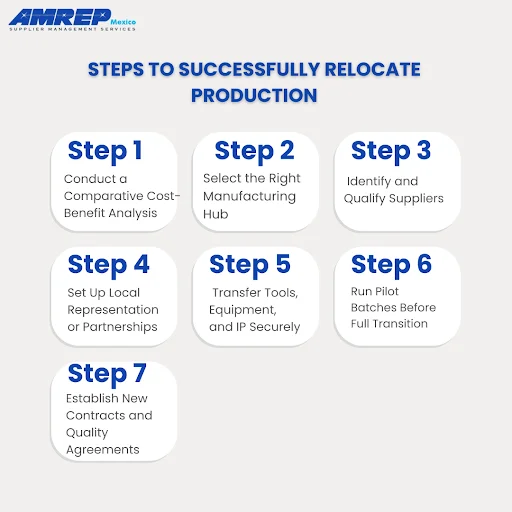
Relocating production is a complex process that requires strategic planning, risk management, and seamless execution to ensure minimal disruption and long-term gains. Below are the key steps every business should follow to ensure a smooth and successful production relocation.
Step 1: Conduct a Comparative Cost-Benefit Analysis
Calculate total landed costs, not just labor rates. Consider material sourcing, infrastructure, tariffs, shipping, and potential downtime during the transition. A detailed cost comparison will validate whether the move delivers long-term savings.
Step 2: Select the Right Manufacturing Hub
Popular industrial clusters in India include:
- Chennai and Bengaluru for electronics and automotive
- Pune and Ahmedabad for engineering and machinery
- Noida and Gurugram for consumer goods and apparel
- Hyderabad for pharmaceuticals and biotech
Choose a location based on proximity to suppliers, labor availability, and logistics infrastructure.
Step 3: Identify and Qualify Suppliers
Use a structured supplier qualification process that includes factory audits, certifications (ISO, GMP, etc.), trial orders, and production capability evaluations. Read our Guide to Qualifying New Suppliers in Malaysia for Manufacturing Success for a comparable process that applies to India as well.
Step 4: Set Up Local Representation or Partnerships
Having a local team or third-party sourcing agent is invaluable for managing day-to-day operations, resolving issues quickly, and ensuring cultural and business alignment.
Step 5: Transfer Tools, Equipment, and IP Securely
Plan the physical relocation of molds, tools, and machinery carefully. Ensure legal protections for your intellectual property are in place before sharing any sensitive designs or technologies.
Step 6: Run Pilot Batches Before Full Transition
Begin with small-scale production to validate supplier performance, product quality, and logistics timelines. Use this phase to refine processes before scaling.
Step 7: Establish New Contracts and Quality Agreements
Create India-specific contracts that address local legal frameworks and include clauses on timelines, penalties, warranty, IP protection, and dispute resolution.
Challenges You May Face and How to Overcome Them
Every production move brings opportunities, but it also comes with hurdles that can impact timelines, costs, and quality. Here are some common challenges businesses encounter during production relocation, along with practical strategies to overcome them.
- Cultural Differences: Business practices in India can differ from those in China. Invest time in relationship-building and clear communication.
- Infrastructure Gaps: While improving, infrastructure in certain regions may still lag behind. Choose established industrial hubs with reliable utilities and transport.
- Regulatory Complexity: Navigating Indian bureaucracy can be slow. Work with experienced legal and compliance advisors to streamline permits and approvals.
- Workforce Training: The skill levels may vary by region and industry. Consider setting up training programs in collaboration with local institutions.
Looking beyond China for production? Discover the best alternatives to manufacturing in China after the April 2025 tariffs.
Case Study: A Mid-Sized US Brand Moves Apparel Production to India
A mid-sized US lifestyle apparel brand shifted its production from China to India to address rising labor costs, shipping delays, and geopolitical uncertainties. After evaluating several countries, India was chosen for its skilled workforce, competitive pricing, strong textile ecosystem, and government incentives. The transition involved selecting a reliable sourcing agent in Tiruppur, conducting supplier audits, running a pilot production, and gradually shifting 70 percent of core SKUs within nine months. As a result, the brand achieved an 18 percent reduction in production costs, improved lead times, enhanced product quality, and better alignment with its sustainability goals. The move allowed the company to diversify risk, improve supply chain resilience, and maintain its commitment to ethical and high-quality manufacturing.
Want to ensure your products meet global standards? Read our comprehensive guide on quality control in manufacturing.
Shift with Certainty: Expert Support for Your Move
Moving production from China to India is not just a tactical shift; it is a strategic decision that can position your business for long-term growth, resilience, and cost efficiency. While India offers compelling benefits, success depends on thoughtful planning, strong supplier relationships, and ongoing quality oversight.
At AMREP, we specialize in supplier audits, quality inspections, and compliance services across Asia. Our experienced teams on the ground in India can help you manage your transition smoothly, reduce risk, and ensure your products meet the highest global standards.
Explore our Supplier Management and Sourcing services to learn how we can support your shift to Indian manufacturing with confidence.